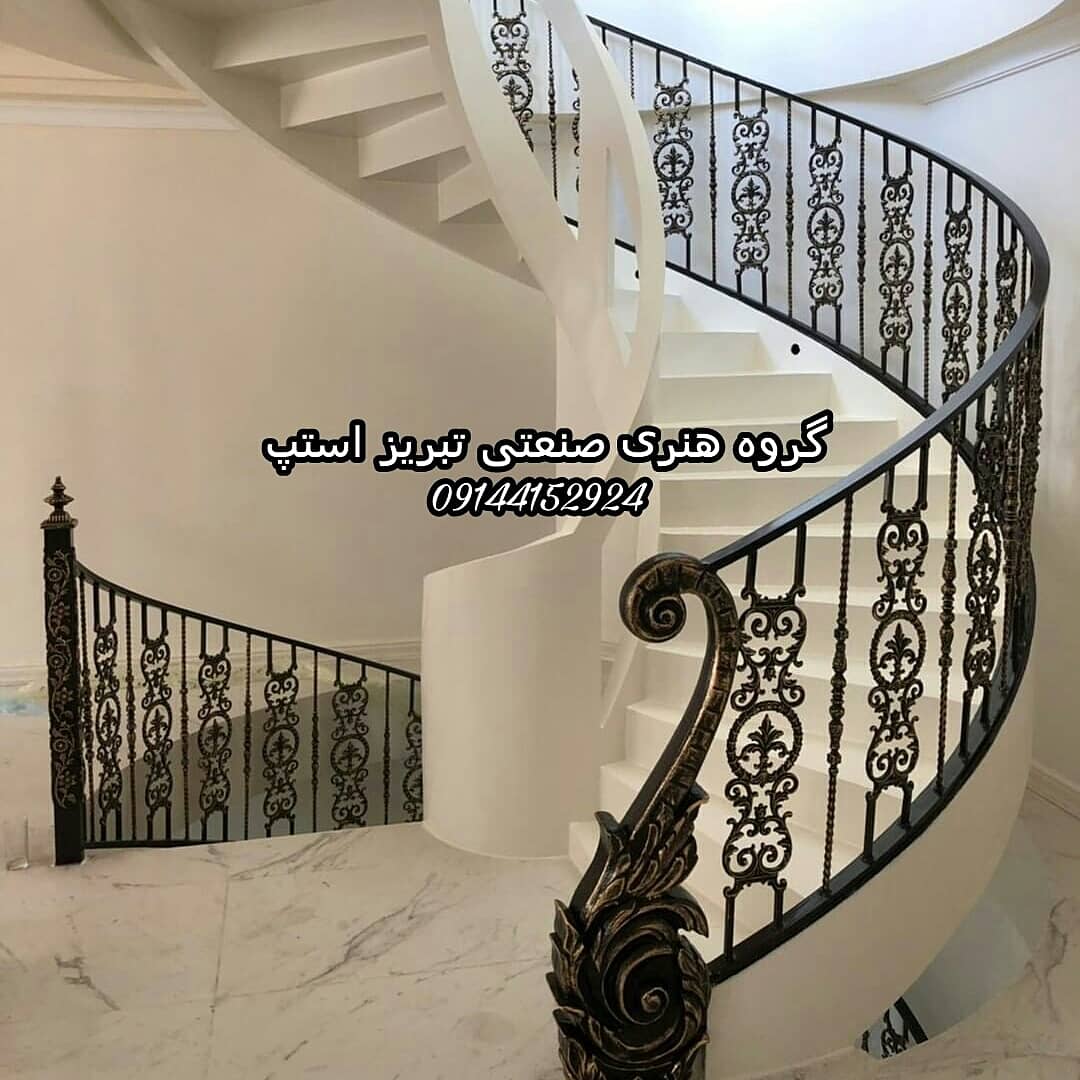
۱۷
شهریور
کوره های ذوب ،آشنایی با کوره ذوب فلزات
انواع کوره های ذوب + فیلم

کوره ذوب
د ۰۹:۴۴ ۶ خرداد ۹۷
زیربنای صنایع سنگین هر کشور، صنایع ذوب فلزات آن می باشد. زیربنای صنایع ذوب نیز صنایع کوره سازی است.
لذا از اینجا به معرفی انواع کوره و اهمیت صنایع کوره سازی توضیح داده خواهد شد
بنابر تعریف یک کوره ذوب وسیله(واحدی) است که قابلیت ایجاد حرارت لازم برای ذوب وزن معینی از فلز یا آلیاژ را با سرعت لازم و هزینه های قابل قبول دارد.
انتخاب کوره با توجه به هزینه، کیفیت فلز، نیازهای تولیدی و نوع آلیاژ تعیین می شود.
انعطاف پذیری کوره در شرایط مختلف، برای انواع تولید مزیت محسوب می شود.
کوره ها از نظر کاربرد به سه گروه پیش گرم، ذوب و نگهدارنده و از لحاظ مصرف انرژی به دو دسته عمده
( سوخت فسیلی ، گرمایش الکتریکی ) تقسیم بندی می شوند.
اما به طور کلی کوره های زیر در ریخته گری وذوب فلزات مورد استفاده قرار می گیرند:
-
کوره های بوته ای (یا زمینی از نوع ثابت و گردان)
-
کوره های تشعشعی (یا روبادده از نوع ثابت و دوّار)
-
کوره های القائی (با فرکانس کم وفرکانس بالا ، همچنین هسته دار (کانالی ) و بدون هسته)
-
کوره های قوس الکتریکی (از نوع مستقیم و غیر مستقیم)
-
کوره های زیمنس – مارتین
-
کوره کوپل
کوره زمینی یا بوته ای
– کوره های بوته ای یکی از متداولترین کوره هایی است که از دیر باز در صنعت ریخته گری سنتی رواج داشته است
و به علت سادگی ساخت ،
ارزانی قیمت و سهولت شرایط کار آن تا به امروز در کلیه ریخته گریهای سنتی به عنوان یکی از کوره های اصلی ذوب فلزات
و در کارخانه های متوسط و بزرگ به عنوان کوره های کمکی ارزش خود را حفظ کرده است.
همانطورکه از نام آنها پیداست برای عمل ذوب از بوته استفاده می شود.
حرارت در این کوره ها بیشتر از طریق هدایت به مواد موجود در داخل بوته انتقال می یابد.
قسمتهای مختلف کوره زمینی عبارتند از :الف) بدنه فلزی ب) صفحه فلزی کف کوره ج) دیواره نسوز د)درب کوره ه) دستگاه دمنده هوا یا ونتیلاتور و) فارسونگاه یا مشعل ز) زیر بوته ای
محاسن کوره بوته ای :
-
قابلیت ذوب فلزات مختلف
-
فراوانی سوخت ( نفت- گازوئیل- مازوت …)
-
اتلاف کم عناصر
-
هزینه ساخت پایین
-
سادگی کار با کوره
عیوب کوره بوته ای:
-
راندمان پایین ۱۰- ۱۵ درصد
-
ظرفیت کم
کوره تشعشعی
-کوره های تشعشعی (شعله ای –روباده ) به کوره هائی گفته میشود
که بین محصول احتراق و مواد شارژ تماس مستقیم برقرار می باشد
و حرارت از سه طریق ، جابجایی ، هدایت و تشعشع به مذاب می رسد.
به عبارت دیگر شعله به صورت جریانی از روی سطح شارژ حرکت میکند و در اثر تشعشع شعله، شارژ ذوب میگردد.
کورههای تشعشعی (انعکاسی)، معمولاً در دو نوع ثابت و دوار (کوره در حین عملیات ذوب، دوران و چرخش دارد)
مورد استفاده قرار میگیرند.
کوره تشعشعی ثابت برای ذوب فلزات و آلیاژهای غیر آهنی به کار میرود.
کورههای تشعشعی نوع دوار به طور گستردهای برای ذوب چدن، با ظرفیتهای ۳۰۰ کیلوگرم به بالا به کار میرود.
سوخت این کوره ها میتواند مایع، گاز و حتی جامد باشد.
ظرفیت این کوره ها بین ۱۵ تا ۷۵ تن متغیر است امّا انواع کوچک آن حتی کمتر از ۵۰۰Kg نیز ساخته شده اند .
از این نوع کوره ها به عنوان نگهدارنده نیز استفاده میشود که ظرفیت آنها تا ۹۰ تن نیز میرسد.
مهمترین مزیتهای کورههای تشعشعی:
-
امکان تهیه مذاب با مقادیر زیاد
-
برخوردای از راندمان حرارتی بیشتر
-
پخش همسان درجه حرارت و ترکیب شیمیایی به دلیل به هم خوردن مذاب
کوره القائی
کوره القائی دستگاهی است الکتریکی که میتواند
با عامل محرکه جریان متناوب به سیم پیچی که دور مواد ذوب شونده فلزی پیچیده شده آن را ذوب کند.
این کوره ها دارای کویل مسی هستند که در اثر عبور جریان الکتریسیته از آن ،
موجب القای جریان الکتریکی بالایی در سطح فلز درون بوته می گردد ،
این جریان الکتریسیته ، حرارت زیادی تولید می کند که منجر به ذوب سریع فلز می شود.
عبور جریان آب در کویل مسی ، باعث جلوگیری از ذوب شدن خود کویل می گردد.
این کوره ها از نظر فرکانس برق مصرفی به سه کوره ، کم ، میان ، وپر فرکانس ، و از نظر نحوه انتقال حرارت
و ماهیت تبدیل انرژی الکتریکی به حرارت ، به دو گروه کوره های کانالی و کوره های بدون هسته تقسیم می شوند.
محدوده فرکانسی عملیاتی کوره از ۵۰ هرتز تا ۴۰۰ کیلوهرتز یا حتی بیشتر میباشد.

کوره قوس الکتریکی
کوره قوس الکتریکی (به انگلیسی: Electric Arc Furnace که به صورت مخفف EAF نامیده میشود)،
شامل یک حمام بزرگ و کم عمق با لایه نسوز اسیدی یا بازی و الکترودهای کربنی بر بالای بستر ذوب می باشد.
هنگامی که کوره با قراضه شارژ شد ، الکترودها پایین آورده می شوند و جریان الکتریکی برقرار می گردد.
سپس الکترودها بالا می روند و قوس الکتریکی از الکترود به فلز برقرار و ذوب شدن آغاز می شود.
دما در نزدیکی نوک الکترود به حدود c◦ ۴۱۰۰می رسد که قراضه را ذوب می کند.
این کوره برای ساخت انواع فولاد از جمله فولاد های ابزار و فولاد های آلیاژی مفید است .
همچنین امکان استفاده از قراضه ارزان را فراهم می کند . مزیت کلیدی ذوب کردن با EAF این است
که امکان تصفیه مذاب و همچنین تولید فولاد های کم کربن وجود دارد.
ایران در زمره ششمین کشور توسعه یافته در بهره گیری از کوره ذوب با استفاده از تکنولوژی قوس الکتریکی قرار گرفت.
تکنولوژی قوس الکتریکی در کوره های ذوب تنها در کشورهای چین، روسیه ، آمریکا ، برزیل و آفریقای جنوبی استفاده می شود.
تکنولوژی قوس الکتریکی دارای این قابلیت است که سیلیکن تولیدی را در دمای بالا تولید کند.
کاربرد کوره قوس الکتریکی شامل موارد زیر است :
-
تولید بسیاری از گریدهای فولاد .
-
میلگرد آجدار تقویت کننده بتن ، انواع مقاطع فولاد تجاری از قبیل ناودانی ، میله و تسمه .
-
گریدهای میله با کیفیت مخصوص مورد استفاده در صنعت خودرو و نفت .
-
منبع متداول تامین مذاب فولاد برای مینی میل های تولید کننده میله یا نوار ورق .
کوره زیمنس – مارتین
حرارت لازم برای ذوب شارژ در کوره زیمنس مارتین توسط گاز و یا سوختهای جامد نظیر ذغال سنگ ویا مایع تامین میشود.
سوخت در دو محفظه احتراق که در دوطرف کوره زیمنس مارتین قرار دارند
محترق شده و از طریق مشعل هایی به کوره زیمنس مارتین وارد می گردد .
دو مشعل قرار گرفته در دو طرف کوره زیمنس مارتین با یکدیگر عمل نکرده
بلکه یکی برای حدود ۱۵ تا ۲۰دقیقه کار کرده وسپس با متوقف شدن ان دیگری برای همین مدت کار می نماید واین عمل به تناوب تکرار می گردد .
مواد شارژ کوره زیمنس مارتین :
-
آهک
-
کلسیم فلورید ( فلوئورین )
-
بوکسیت ها
-
آجرهای شکسته ی شاموتی
-
سنگ آهن
-
قراضه فولاد
- چدن خام
کوره کوپل
کوره کوپل متداولترین وسیله ذوب چدنهاست. بعد از کوره زمینی مرغوبترین چدن نسبت به کورههای دیگر از این کوره تهیه میشود.
این کوره در ۴۰۳–۲۲۱ قبل از میلاد در چین برای اولین بار ساخته و مورد استفاده قرار گرفت.
کوره کوپل دارای مکانیزم عملکرد ساده بوده و بیشتر برای ذوب قراضه های چدنی استفاده می شود.
همچنین نحوه کار این کوره با کوره بلند شباهت زیادی دارد. تفاوت آنها در این است که کوره بلند برای احیای سنگ معدن آهن استفاده می شود.
این نوع کوره ذوب در اندازه های متنوع و با قدرت ذوب بین ١٠٠ کیلوگرم تا چند ده تن چدن وجود دارد .
کوره کوپل به طور ساده به دو بخش اساسی تقسیم می شود :
۱_ ساختمان اصلی که شامل بدنه فلزی، مواد نسوز، محل شارژ، ورودی هوا و خروجی مذاب می شود .
۲_ بخشهای جانبی که شامل محل توزین شارژ، تصفیه گازهای خروجی، پیش گرم هوا وریل شارژ می گردد .
منبع:فولاد مهر/دانشمند
نظرات